In our space of producing world-class Abrasive Wheel Blast equipment everything begins with our customer….
Abrasive Wheel Blast Automation Explained
While we may have our own thoughts and extensive capabilities on what automation is, it really depends on what our customer’s definition is. From application, to part, to production targets, the open communication on the front end is critical. These early conversations set the direction for the project. Historically our automated equipment provides all the benefits you could imagine – increased production, repeatability, improved quality, etc.
Now, in our challenging time of labor shortages, the need to automate and do more with less is more important than ever. The end goal for us is to always provide the safest and most efficient machine possible while meeting all the customer’s requirements for the system. Whether it is one of our standard automated systems, a completely custom automated system or something in between.
When Is Automation the Right Solution?
Some customers come to us asking for automation when all they really need is a standard machine with modifications to handle their specific requirements. Other times we get requests for standard machines, but as we flush out the details of the application, we may recommend an automated or modified solution for maximum profitability.
It all starts with a conversation and a customer’s part, along with mutual collaboration. In the early stages it is more art than science. While we consider ourselves experts within the Wheel Blast System industry, there are many things we need to know in order to get started on the correct path. Are there any applicable specifications to follow? Are there any current in-house procedures to be followed? Do they have their own validation process? Just to name a few. These basic questions are indicators to provide an initial direction.
As the process evolves it turns into more of the science component, providing technical solutions to the application. Some situations require us to develop completely new processes which we are able to test in our demo lab for proof of concept.
What to Expect from On-Site Testing Vs. Theoretical Models
Empire Wheel Blast Systems has our own Demonstration Laboratory. We have the appropriate equipment to provide real life testing of sample parts to prove the results we determined are achievable through the collaboration phase. There is a formal digital documented process we follow to secure parts and manage the process. We have fully trained Technicians on-site that conduct the entire trial, providing full documentation, ultimately providing a comprehensive report of the results.
Everyone’s time is valuable, but, when possible, we invite and highly encourage our customers to be present during the trial portion. This way continued collaboration can take place, on the spot. Details may need to be adjusted, and can be done immediately, providing continued efficiencies.
The Future of Abrasive Wheel Blast Automation
We all know technology is evolving faster than it ever has before and as various technologies continue to come to the forefront, they will certainly be incorporated into the Wheel Blast Systems. We are already seeing this in world of Abrasive Blasting with the incorporation of robotics, IOT, and HMI digital controls. We were early adopters to all of these technologies, and we are very much looking forward to the future innovative solutions we will be able to provide our customers.
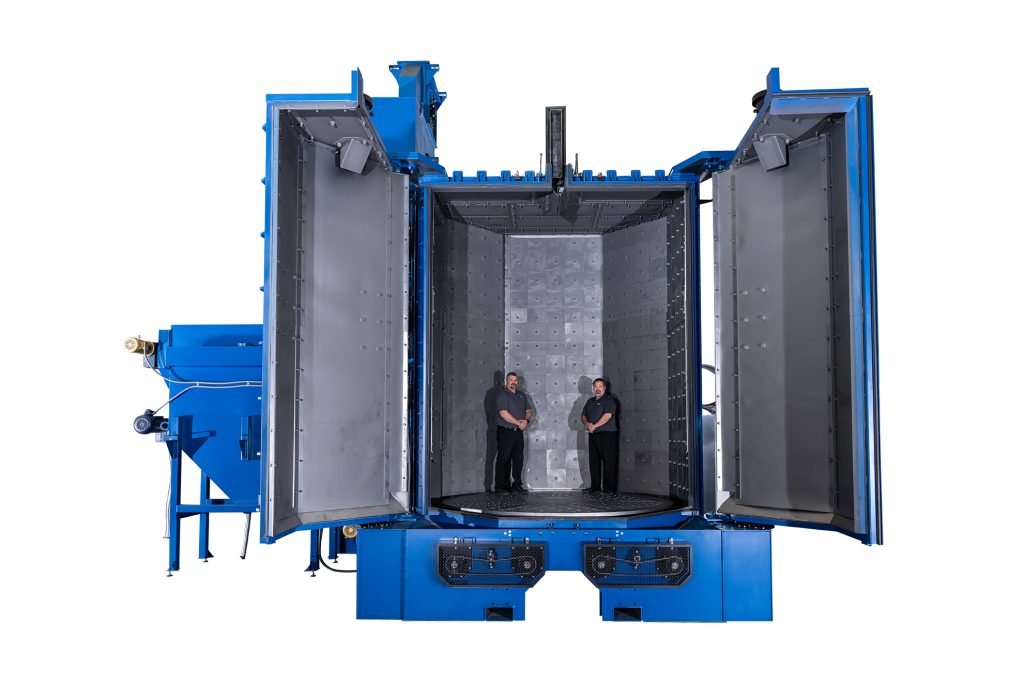
One trend we are seeing is the need to provide automated Abrasive Wheel Blast systems for larger parts. In the past there have been limitations based on weight and part size on what could be accommodated with this type of technology. Up until recently air blast rooms have long been the industry standard for abrasive blasting of large parts up to 10’ x 12’ simply due to the scalability offered when enclosing the human operator within the blast chamber.
We wanted to challenge ourselves and ask, “What if there is a better way?”. So, we developed our TB120 Series in response to customer demand. We now offer a new TB120XT Table Blast System that literally takes the operator out of the blast room. This system features a 120” diameter, 10,000 lb. capacity manganese steel turntable, dual front swing doors, and two 15” diameter 20 HP Direct Drive Blast Wheels. In addition, the TB120 is designed with a notched top for center crane loading and unloading. And, operational parameters are imputed via a 7” Touchscreen HMI located on the electrical control panel.
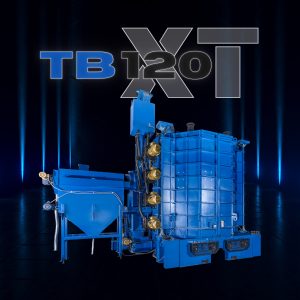
This particular system offers high versatility and efficiency in processing complex workpieces from large parts to heavy fabrications. The two blast wheels propel abrasive by centrifugal force through a controlled blast pattern. The 120” diameter turntable rotates at 5 rpm to provide 360-degree exposure to the blast stream. A Mechanical Reclaim System recovers spent media using a Bucket Elevator and a 20” Gravity Lip Separator to remove fines.
Automated wheel blast equipment of this size provides the relatively mature abrasive blasting industry with an exciting new alternative that satisfies a high demand in the industry for alternatives to the incumbent air blast room technology. Often, we have our customer bring in their parts for the factory acceptance testing (FAT) phase. It’s always fun to see their reaction and excitement when they see the before and after results. It is often disbelief when they see what can be accomplished with the equipment from both a productivity and finish perspective.
The Empire Difference in Automated Wheel Blast Solutions
The other critical factor our customers are asking for is the need to find partners who have a thorough understanding of the industry with an established process to manage projects that can often be quite sophisticated pieces of equipment. In our world, close is not good enough. Collaboration with the customer is key – not just during the discovery phase but through every step of the production process, including project verification meetings, approval drawings, FAT, system installation, and follow up by our team after the installation is complete and the equipment is up and running. We understand these are significant investments our customers are making and our intention is to assure them we will be with them every step of the way. It’s what we like to call the Empire Difference.
There are a number of things that go along with that but it comes down to the point that we are a process driven organization. Once we are awarded a job, a Project Manager is assigned to it and has full responsibility of being sure the process stays on track all the way through installation. There are milestones we achieve and communicate with the customer regularly to keep them involved with the progress. It is absolutely a partnership to be certain all requirements and expectations are met.